3D Challenges in the Fashion Industry
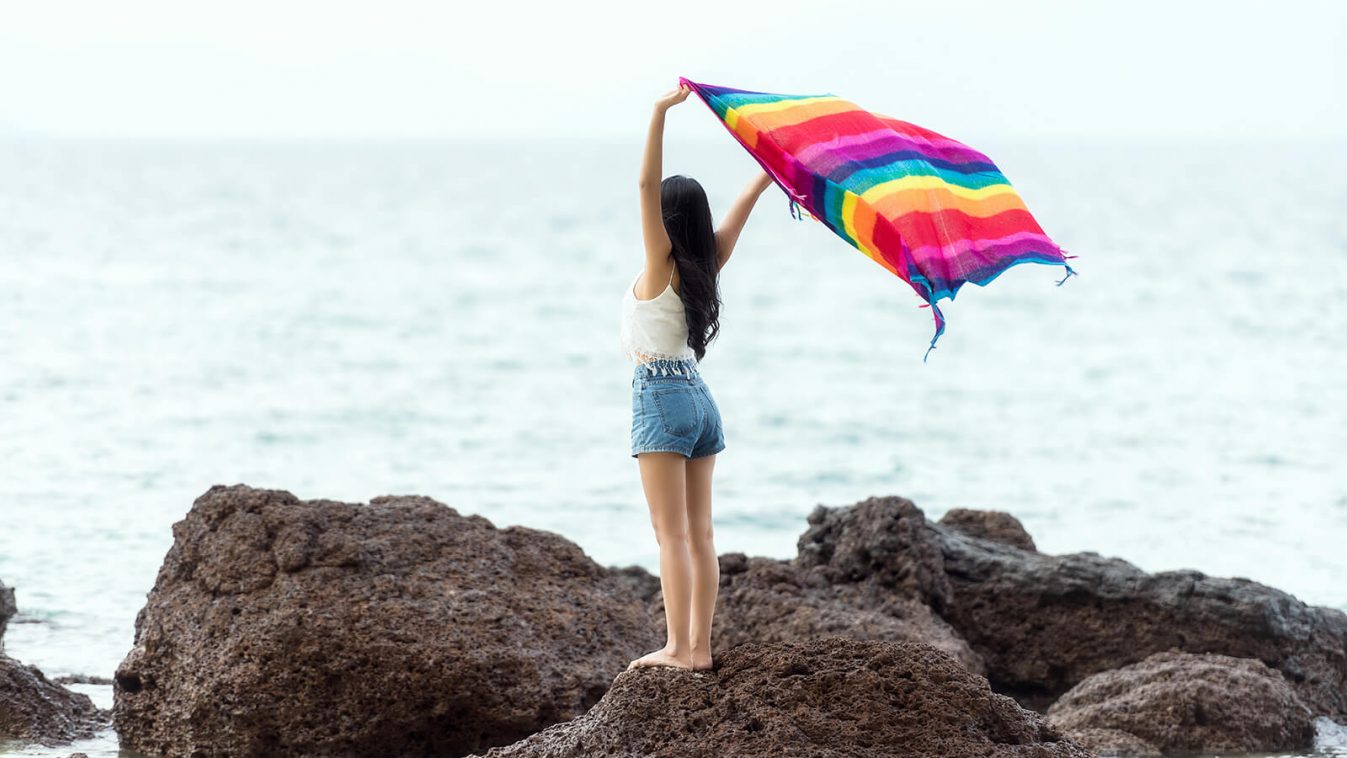
Leggi in ItalianoLire en FrançaisLeer en Español
Fabric and garment simulation raise some very real challenges in today’s fast-paced fashion design and manufacturing industry, such as mechanical simulation, collision detection, geometric modeling, interactivity, and others.
Let’s start by looking at how a fabric reacts under various conditions – draping, folds, wrinkling, and tearing. A fabric’s reaction to these and other conditions is the result of the many properties that make up specific fabrics.
More importantly, is how a fabric reacts to its environment, where certain fabrics will react very differently, for example, what a fabric looks and stretches under wind conditions, and under different light conditions. The garment itself also has to follow the shape and movements of the human body. Therefore, creating the appropriate fabric simulation must take these properties into account.
Fabric simulation has gone through several phases. Back in 1975, fabric could be modeled as a deformable surface exhibiting various properties, such as elasticity, viscosity, and plasticity. In the early 1990s, simulation accurately generated wrinkles in a piece of fabric, but was unable to model the draping of the cloth in more complex scenarios. However, this technology required excessive computation time for complex shapes, and was not adapted to garments that inherently had complex shapes.
3D is gaining momentum in the fashion industry
Over the past decade, 3D technology has made significant progress, and the fashion and apparel industry is integrating 3D into its design processes. Many retailers and brands use 3D visualization, virtual sampling to optimize workflows, boost product development, and enable personalization, and have adopted 3D to visualize products in the design and fitting stages. As a result, decision-makers can choose the best possible combinations, and sell their products to wholesalers, significantly reducing the number of physical samples.
Although the use of 3D can offer numerous benefits, convincing leading brands to abandon traditional practices, is tricky. This is especially true in an industry where the top players continue to host lavish and costly fashion shows to launch new collections and produce reams of prototypes.
The critical consideration of any 3D representation is, therefore, its true-to-life visualization capability – accurate 3D fabric/garment rendering. True-to-life visualization cannot exist without advanced fabric testing, measurement, and analysis tools to capture the physical and visual properties of a given fabric.
A study conducted by the Fashion Design Department at Anadolu University, Turkey, confirms the clear advantages of using a CAD system as compared to manual pattern preparation methods, noting that it is “easy, fast, and cost-effective.” The study also found that the number one challenge in the application of 3D systems in textiles and garments, is the draping. Despite the positive results, it is clear that to improve rendering quality, more information about the fabric is required.
True-to-Life 3D Renders for the Fashion Industry
To achieve true-to-life simulations, you need to combine 3 fundamental elements in the creation of a 3D garment: the body shape you want to dress, the pattern geometry of the model, and the information about the fabric, such as behavior and visual properties.
Capture the fabric properties
Optitex’s Fabric Measurement solution offers a variety of tools to measure most fabric properties, such as stretch, shear, stiffness, and others. Fabrics can also be scanned in U3M format to capture their visual properties – colors, structure, reflectance, and transparency.
Measuring fabrics may seem like a lengthy process, but it’s just a matter of minutes. Each fabric measurement enriches the fabric database and can be shared with all users and stakeholders in the supply chain.
The latest version of Optitex 3D Pattern Design Software (PDS), V O19.4, can import the fabric and its properties, and accurately render a piece of fabric or finished garment in 3D, maintaining the shape of the avatar, the style, and the properties of fabric under specific conditions.
Sharing explicit 3D representations of your ideas will allow you to improve collaboration and communication between your teams, to reduce the number of prototypes needed to validate a new model, thus making the creative process faster and more sustainable.
To learn more: https://youtu.be/a416xfe2A1Y
References:
- Comparison of real garment design and 3D virtual prototyping, Esra Öğülmüş at Independent Researcher, Mustafa E. Üreyen at Eskisehir Technical University, Eskisehir
- 3d cloth and fabric material tutorial, March 2017
- 3d technology a new dimension for fashion, July 2019, Medium.com
- Virtual Clothing/ Theory and Practice – Pascal Volino, Nadia Magnenat-Thalmann – This is taken from an entire book. Is there a section/passage you wish to quote or reference?