Printing on Demand is Here
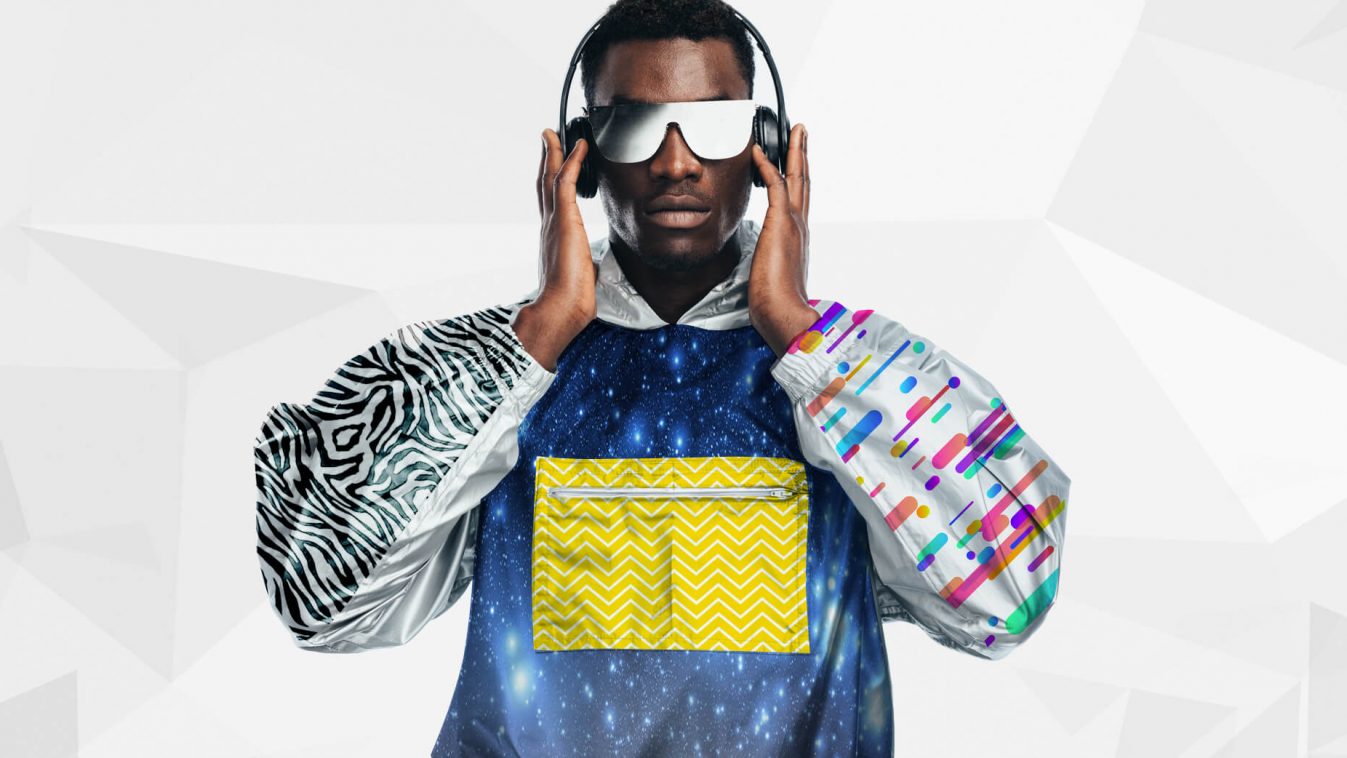
In a recent article, Textile Today magazine described digital textile printing as “one of the most promising developments in the textile industry.”
The most common method of textile printing is screen printing using rotary frames, but with the introduction of digital printing in the 1990s, the time gap between the design of the print and the production of the finished product became significantly shorter.
A few years ago, digital textile printing was only competitive for sampling, but this situation has changed dramatically with the appearance of new printers and inks.
The digital textile printing process consists of applying the prints directly to the white fabric. Two of the most important factors, which differentiate digital printing from traditional methods are #personalization and #evolution.
In this post we have chosen to examine the technology of digital textile printing and its progress in the current fashion world.
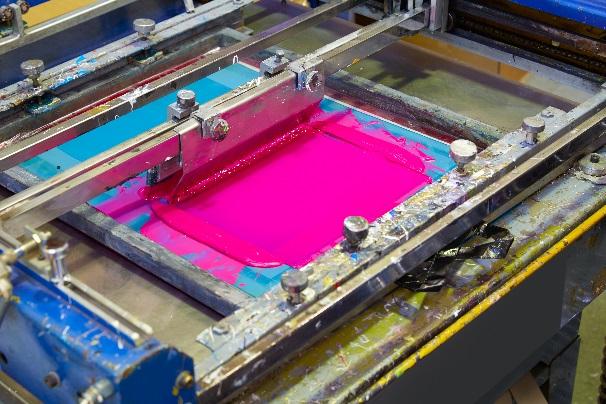
Serigraphy printing
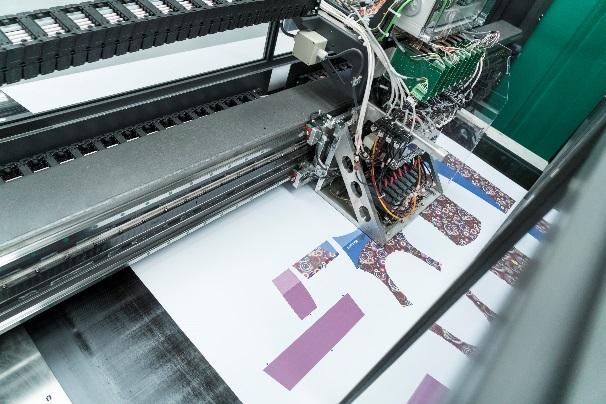
Digital Printing
Let’s take a closer look at some of the advantages of digital textile printing.
- Shorter production times: Traditional screen printing can take up to eight weeks to complete and require several procedures to obtain a perfect final result. Digital inkjet printing enables an immediate, single-step production on the same fabric.
- Unlimited color and visual integrity: Digital printing provides access to an unlimited range of colors and patterns, as well as high-fidelity renderings. This allows retailers to print any design imaginable and stay true to specific brand colors.
- Eco-friendly: Not only does digital printing reduces the amount of fabric waste, it uses up to 95% less water and 75% less energy than traditional screen printing.
- Shorter runs and smaller collections: Designers can create just a few hundred pieces and then vary the colors or move on to the production of another entirely different model. This helps reduce waste and allows retailers to meet the latest trends quickly.
- Personalization: Today’s buyers, especially of younger generations, want to co-create and personalize their purchases. With digital printing, cost-effective personalization quickly becomes a reality.
Print & Cut by Optitex is a comprehensive software solution that allows us to print and cut the pieces of a garment directly on white fabric.
How is this possible? The 5 step process is straightforward:
- Make the pattern using Optitex PDS
- Prepare graphics for printing with Adobe Illustrator
- Create marker with Optitex Marker and generate print & cut output files
- Print the fabric with digital fabric printer
- Cut the product pieces with a single-ply cutter
The potential of digital printing for the fashion industry goes far beyond increased creativity, faster production, and profitable business models. This advanced technology also enables data collection and the creation of a new and improved customer experience.
Benefits include:
- Shorter production times
- Unlimited color and visual integrity
- Sustainability
- Shorter runs and smaller collections
- Personalization
The solution: Print & Cut, a simple and straightforward software solution.